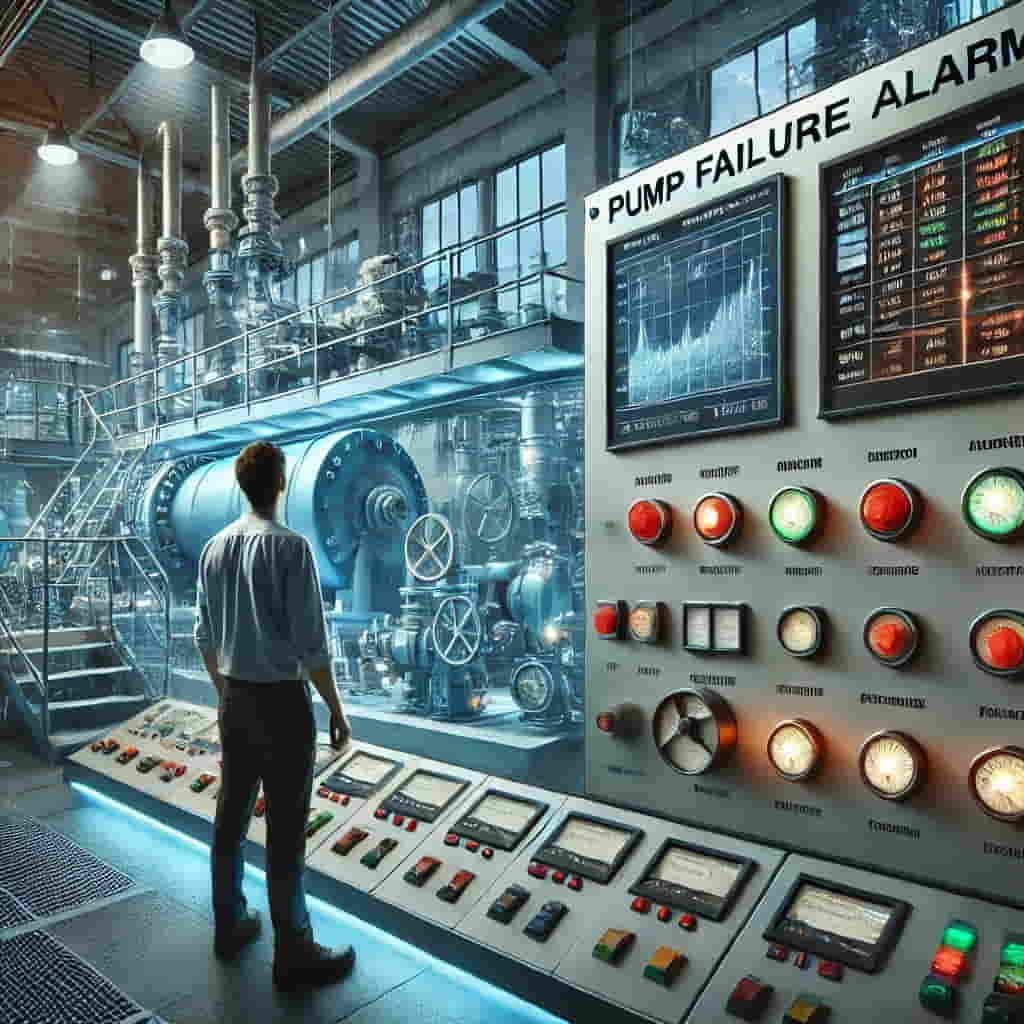
It’s 3 a.m. on a Tuesday, and you’re snug in bed, catching up on much-needed rest. Meanwhile, miles away, in the quiet darkness of an industrial facility, a sump pump quietly churns away, keeping groundwater at bay. It’s just another night at work—until it’s not. Suddenly, that pump sputters, groans, and fails. The water level starts to rise. Without a reliable pump failure alarm, this minor issue could spiral into a costly nightmare by dawn.
If you’re a facility manager, the last thing you want is to walk into work to discover a basement full of water and expensive machinery submerged and damaged beyond repair. Yet, this is a scenario many industrial facilities face because of overlooked pump failure alarms. Let’s dive into how pump failure alarms can be your unsung heroes, preventing costly downtime and ensuring your operations keep flowing smoothly.
The Invisible Guardian: Why Pump Failure Alarms Matter
Think of a pump failure alarm as a smoke detector for your facility’s pumping systems. You wouldn’t dare run a facility without a smoke detector, right? So why take the risk with your sump pump system?
Water is a formidable enemy in industrial environments. It doesn’t just cause damage; it halts production, destroys equipment, and can create hazardous conditions. A pump failure alarm is designed to detect issues like pump malfunction, overflows, or power outages and alert you before these problems escalate into full-blown crises.
Consider this: According to the National Flood Insurance Program, just one inch of water can cause up to $25,000 in damage to a building. Now, multiply that by the cost of lost production, damaged goods, and emergency repair bills. It’s easy to see how a pump failure could set off a chain reaction of expensive problems. But with a pump malfunction alarm in place, you get an early warning that allows you to take swift action, potentially saving thousands of dollars.
Real-World Examples:
Let’s look at the case of a large pharmaceutical manufacturing plant in the Midwest. A routine maintenance check missed a critical issue in the sump pump system. Without a pump failure alarm in place, a severe storm overwhelmed the system, leading to catastrophic flooding. The result? Over $1 million in damages, lost inventory, and weeks of halted production. This example isn’t an isolated incident; many industries, from automotive manufacturing to food processing, have faced similar crises simply because they lacked an effective pump failure alarm system.
The Anatomy of a Pump Failure Alarm
So, how does a pump failure alarm work? The system is ingeniously simple yet highly effective. When your sump pump is working as it should, the alarm remains silent. But if it detects an issue—such as a pump that fails to start, runs continuously without shutting off, or encounters an electrical fault—the alarm activates. Depending on the system, this could be a loud audible alarm, a flashing light, or even a cellular notification sent straight to your phone.
Technical Depth:
Let’s dive deeper into the technical aspects. Pump failure alarms often use a variety of sensors, each with a specific role:
- Float Switch Sensors: These detect rising water levels and activate the alarm if the pump isn’t working correctly.
- Pressure Transducers: These measure the pressure within the pump system, signaling an alarm if the pressure falls outside the normal range.
- Current Sensors: These monitor the electrical current drawn by the pump, identifying anomalies that could indicate a pump fault.
The sensitivity of these sensors is crucial. For example, a high-quality float switch sensor can detect water level changes within fractions of an inch, providing early warnings even for minor pump malfunctions. Understanding the types of sensors and their sensitivities can help you choose the right system for your facility’s needs.
Preventing Downtime: The Real Cost-Saver
Downtime is the enemy of productivity. In industrial facilities, every minute your operations are offline translates to lost revenue, missed deadlines, and unhappy clients. It’s not just the cost of repairs; it’s the ripple effect on your entire business.
Cost-Benefit Analysis:
Let’s break down the costs associated with pump failures versus the cost of implementing a pump failure alarm system. Suppose the average cost of a pump failure alarm system is $500, including installation. On the other hand, consider the potential costs of a pump failure:
- Direct Damage Costs: $25,000 for water damage to equipment and infrastructure.
- Lost Production Time: $10,000 per hour of downtime (assuming a small facility), with repairs taking at least 5 hours.
- Repair Costs: $5,000 for emergency pump repair and replacement.
Even in this conservative estimate, the costs of a single pump failure without an alarm system can easily exceed $80,000. Compare this to the relatively minor investment in a pump failure alarm, and the cost-benefit ratio is clear.
Maintenance and Troubleshooting: Ensuring Longevity
Pump failure alarms are only as effective as their maintenance. Regular checks are essential to ensure they remain functional:
- Weekly Testing: Regularly test the alarm system by simulating pump failure scenarios. This can involve manually lifting the float switch or disconnecting the power supply to the pump.
- Sensor Calibration: Periodically calibrate sensors to ensure they maintain their sensitivity. Over time, sensors can drift, leading to either false alarms or missed warnings.
- Battery Replacement: For alarms with battery backups, replace batteries annually or as recommended by the manufacturer.
Troubleshooting Common Issues:
- False Alarms: These can often be caused by sensor malfunctions or environmental factors like humidity. Ensure sensors are properly shielded and check for any wiring issues.
- No Alarm Activation: If the alarm doesn’t activate during testing, it could be due to a faulty sensor, depleted battery, or wiring problems. Address these issues immediately to maintain the system’s reliability.
Environmental Impact: A Hidden Cost
Beyond the immediate financial implications, pump failures can have severe environmental consequences. A failed sump pump in an industrial setting can lead to significant water contamination, especially if the water contains chemicals or other hazardous materials. This not only leads to hefty fines and cleanup costs but can also damage the local ecosystem.
Regulatory Compliance:
Many industries are subject to strict environmental regulations that mandate the prevention of water contamination. The Environmental Protection Agency (EPA) has stringent guidelines on water discharge, and failure to comply can result in severe penalties. Implementing a pump fault alarm system can help ensure your facility meets these regulatory requirements, providing a safeguard against accidental spills and leaks.
Future Trends: The Evolution of Pump Failure Alarms
The future of pump failure alarms lies in connectivity. Traditional alarms are still valuable, but as facilities become more automated, the demand for smarter, connected systems is rising. Enter the cellular sump pump alarm monitoring system.
Emerging Technologies:
The integration of the Internet of Things (IoT) and Artificial Intelligence (AI) is revolutionizing pump failure alarms. IoT-enabled sensors provide real-time data, allowing facility managers to monitor pump performance from anywhere. AI algorithms can predict pump failures before they happen by analyzing patterns in the data, enabling proactive maintenance.
These advancements are not just about convenience—they’re about creating smarter, more efficient facilities that can operate seamlessly with minimal human intervention.
Conclusion: An Ounce of Prevention…
As the saying goes, “An ounce of prevention is worth a pound of cure.” In the world of industrial facility management, this couldn’t be more accurate. Pump failure alarms are that ounce of prevention, giving you the early warning needed to avoid costly repairs, extensive downtime, and the headaches that come with them.
By investing in a reliable pump failure alarm system, you’re not just protecting your facility—you’re ensuring its productivity and success. So, the next time you’re reviewing your facility’s safety measures, don’t overlook the humble pump failure alarm. It might just be the difference between a minor fix and a major financial disaster.
In short, when it comes to managing an industrial facility, it pays to be proactive. And with a pump failure alarm in place, you can rest easy, knowing that your operations are protected around the clock.