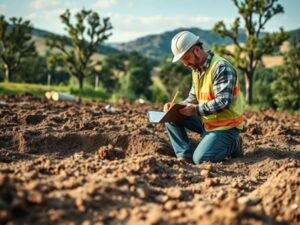
Picture this: You’re finally standing on that perfect plot in Horseshoe Bay, TX—sun dancing off the lake, a light breeze tugging at the oak trees, and the faint sound of construction humming in the background. It’s the beginning of your dream custom home. You’ve spent months (maybe years) envisioning every detail—from the granite countertops down to the custom crown molding. But lurking behind all that excitement? A nagging thought: What if something goes wrong?
You’re not alone. Many homeowners share the same quiet fears—poor workmanship, shortcuts behind the walls, ballooning costs, or worse, structural issues that don’t rear their ugly heads until years later. Fortunately, there’s one safeguard you can control: Quality Assurance (QA).
This guide unpacks everything you need to know about QA when working with custom home builders in Horseshoe Bay, TX—arming you with the confidence to protect your investment, ensure top-tier craftsmanship, and enjoy peace of mind from groundbreaking to move-in day.
What Exactly Is Quality Assurance in Custom Home Building?
Think of Quality Assurance as your home’s invisible shield. It’s not a single inspection or a quick walk-through. It’s an ongoing, deliberate process embedded at every stage of the build—from the drawing board to the final coat of paint.
Here’s how it differs from a standard home inspection:
- Quality Assurance is proactive. It’s a systematic approach involving planning, material vetting, and detailed checkpoints during construction.
- Inspections, while important, are reactive. They typically happen at the end of key phases to catch problems after the fact.
In short, QA prevents mistakes. Inspections merely identify them—often when correcting them becomes costly and stressful.
Why Quality Assurance Is Crucial in Horseshoe Bay, TX
Now, building anywhere requires QA, but Horseshoe Bay’s unique environmental and regulatory landscape makes it absolutely essential.
1. The Climate Challenge: Horseshoe Bay’s hot summers, sudden storms, and high humidity levels can wreak havoc on poorly constructed homes. If quality control is neglected, water vapor can sneak into walls, attic spaces, and crawl spaces—leading to mold, wood rot, or warped flooring. A QA-driven builder knows how to integrate moisture barriers, properly ventilated roof assemblies, and waterproofing membranes from day one.
2. The Soil Factor: Here’s where Horseshoe Bay homes face a silent enemy: expansive clay soils. These soils swell when wet and shrink when dry, causing homes without well-engineered foundations to shift, crack, and settle unevenly. Builders committed to QA take this seriously by:
- Conducting professional geotechnical soil testing to identify how reactive the clay is on your specific lot.
- Designing foundations based on that data—often opting for post-tensioned slabs or pier-and-beam systems that anchor deeper into stable ground, minimizing movement.
- Applying soil stabilization techniques such as lime treatment to reduce soil expansion.
- Installing proper drainage systems and grading to control moisture levels around the home’s perimeter, preventing water pooling near the foundation.
Without these steps? The foundation—and your dream home—could literally buckle under pressure.
3. HOA & Local Compliance: Horseshoe Bay’s luxury neighborhoods pride themselves on uniformity, safety, and aesthetics, backed by strict HOA guidelines. Builders who follow a rigorous QA process ensure:
- Every element, from exterior finishes to roof heights, aligns with HOA standards.
- Timely communication and documentation submission to avoid fines or redesigns.
- Compliance with local codes for safety, energy efficiency, and storm resilience.
The Quality Assurance Process—What a Solid QA Program Looks Like
A reputable custom home builder in Horseshoe Bay, TX will have a well-oiled QA process that includes these key stages
1. Pre-Construction Planning
The foundation for success starts before a shovel hits the ground:
- Soil Analysis: Engineers evaluate the lot’s soil composition. If the clay is highly expansive, the foundation design is adapted accordingly, often reinforced with steel and tension cables or piers drilled deep into bedrock.
- Blueprint Detailing: Each blueprint outlines exact material grades, fastening methods, and local code specifications, leaving no room for vague assumptions.
- Permit & HOA Approvals: Builders double-check all necessary approvals are secured before work begins, ensuring no last-minute compliance surprises.
2. Material Verification
Materials are the bones of your home. QA-minded builders go beyond supplier invoices:
- Lumber Checks: Moisture content is measured to prevent future warping. Only kiln-dried, grade-stamped lumber passes.
- Concrete Mix Validation: Builders ensure the concrete used meets PSI strength requirements (especially important for load-bearing foundations in clay-heavy soils).
- HVAC System Sizing & Verification: Horseshoe Bay’s climate demands properly sized HVAC systems—not just “big enough,” but optimized. Oversized units cause short cycling, increasing wear and energy bills. Builders conduct a Manual J load calculation, factoring in window placement, insulation, and square footage to get the sizing just right.
3. Workmanship Checkpoints
Construction isn’t a one-and-done process. Builders focused on QA insert structured, multi-phase checkpoints:
- Framing Inspections: Verifying that framing adheres to precise measurements and fastening techniques, ensuring structural integrity.
- Rough-in Checks (Plumbing, Electrical, HVAC): Ensuring systems are properly routed, secured, and meet Horseshoe Bay’s strict code requirements.
- Moisture Barrier Tests: Before insulation or drywall goes up, barriers are examined to confirm there are no weak points vulnerable to Texas storms or humidity.
4. Third-Party Inspections
Here’s where great builders set themselves apart. They bring in licensed, independent inspectors—people with no stake in cutting corners—to verify each stage:
- Foundation integrity.
- Mechanical system placement.
- Roofing and exterior waterproofing.
Their reports give homeowners hard evidence of quality, phase by phase.
5. Post-Construction Documentation
Once the dust settles:
- Detailed Punch Lists: Any minor defects or adjustments are addressed and signed off before final payment.
- Warranty Packages: Reputable builders offer structural warranties (often 10 years), workmanship warranties, and manufacturer-backed material guarantees.
- Maintenance Guides: QA doesn’t stop at move-in. Homeowners are provided tailored guides based on Horseshoe Bay’s climate—think gutter cleaning schedules, HVAC service intervals, and foundation watering tips.
Empower Yourself: Questions You Should Ask Your Builder About QA
Not sure how to gauge if your builder has a robust QA process? Here’s a starter checklist:
- “What specific QA steps do you follow during each construction phase?”
- “Do you conduct geotechnical soil testing for every lot?”
- “How do you adapt foundation designs based on Horseshoe Bay’s soil conditions?”
- “Can you show documentation verifying material grades (e.g., lumber moisture readings, concrete strength tests)?”
- “Do you use third-party inspectors? At which stages?”
- “What’s your process for HVAC sizing calculations tailored to this climate?”
- “Can I see examples of warranty and post-build maintenance documentation from past projects?”
If responses feel rushed or vague? That’s a red flag worth heeding.
Illustrative Scenario: Two Homeowners, Two Outcomes
Let’s call them Lori and Mark. Both hired custom home contractors in Horseshoe Bay, TX to build their dream homes. But their stories couldn’t be more different.
Lori chose a builder based purely on price and timeline promises. No soil test was done. Her builder used generic foundation plans designed for different soil types. No third-party inspections, no material verification. Two years later, her foundation has settled unevenly, doors stick, and water seeps in after storms. Repairs? Tens of thousands of dollars, constant stress, and lowered resale value.
Mark, however, prioritized QA. His builder tested the soil, designed a reinforced slab-on-grade foundation to counteract clay movement, used verified materials, and involved third-party inspectors at every stage. Three years on, his home stands solid, utility bills are low thanks to right-sized HVAC systems, and the house commands premium value in resale discussions. Zero maintenance nightmares.
The difference? Quality assurance.
Common QA Pitfalls (And How to Spot Them Early)
Here’s what savvy homeowners in Horseshoe Bay should watch for:
- Vague Contracts: If QA steps, inspection schedules, or material specs aren’t clearly outlined, question why.
- Overpromising Timelines: Unrealistic build times often signal corner-cutting.
- No Soil Testing Clause: In Horseshoe Bay, skipping geotechnical testing is reckless.
- Minimal Communication: If builder updates lack detail or documentation, chances are, so does the construction process.
Your Home, Built Right the First Time
At the end of the day, building a custom home in Horseshoe Bay, TX isn’t just about the stunning views or elegant finishes. It’s about ensuring the foundation—literally and figuratively—is rock solid.
By understanding the nuts and bolts of Quality Assurance, and knowing exactly what to demand and expect from your builder, you’re not just protecting your investment—you’re crafting a home designed to stand the test of time, stress-free.
Because your dream home deserves nothing less.